Warum ist die Lebensmitteldose eigentlich rund und hat Rillen? Hier findest du die Antwort.
Wie aus Stahl Weißblech gemacht wird – ein Besuch bei thyssenkrupp Rasselstein
thyssenkrupp Rasselstein ist Deutschlands einziger Hersteller von Weißblech. In seinem Werk in Andernach produziert das Unternehmen verzinntes und spezialverchromtes Feinstblech – auch Weißblech genannt. Das ist, je nach Anwendungszweck, zwischen 0,100 und 0,499 Millimeter dick beziehungsweise eher hauchdünn. Zusammen mit Dr. Peter Kirchesch, Experte für Nachhaltigkeit bei thyssenkrupp Rasselstein, haben wir uns angeschaut, wie aus Stahl Weißblech hergestellt wird.
Um den gesamten Prozess der Herstellung zu verstehen, muss man bei thyssenkrupp Steel in Duisburg beginnen. Hier entsteht das Ausgangsmaterial – der Stahl. Roheisen aus dem Hochofen und Stahlschrott werden im Stahlwerk zu Rohstahl verarbeitet. Der Rohstahl wird zunächst in sogenannte Brammen vergossen. Das sind schwere Stahlblöcke. Das Material wird warm gewalzt, bis es zwischen 1,5 und 3,8 Millimeter dünn ist und in Rollen, zu sogenannten Coils, aufgewickelt werden kann. Als Coil kommt das Material in Andernach, dem Standort von thyssenkrupp Rasselstein, an.
Warmgewalztes Stahlband – das Ausgangsmaterial von Weißblech
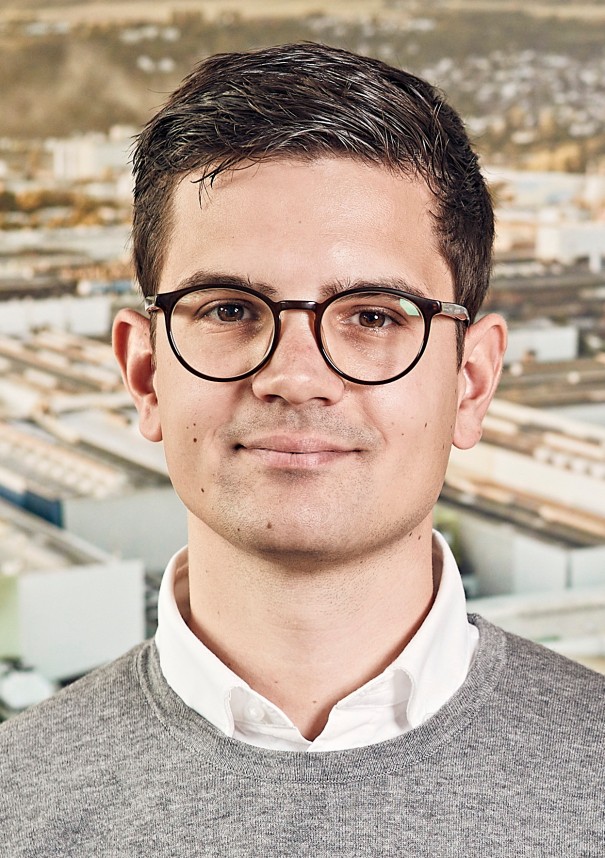
Noch ist das Material zu dick, um zu Lebensmitteldosen, Kronenkorken, Verschlüssen oder Aerosoldosen verarbeitet zu werden. Daher wird die Banddicke in der Kaltwalzanlage auf bis zu 0,10 Millimeter reduziert. „Das ist einer unserer Kernarbeitsschritte“, erläutert Kirchesch und fügt hinzu, dass das Warmband insgesamt eine Dickenreduktion von bis zu 90 Prozent erfährt. „Damit das bei hoher Geschwindigkeit gelingen kann, muss der Walzspalt, also dort, wo das Band durchläuft, mit einem Gemisch aus Walzöl und Wasser geschmiert werden.“ Im nächsten Arbeitsschritt wird diese Emulsion beim Entfetten wieder entfernt.
Haubenglühen und Durchlaufglühen
Die enormen Kräfte beim Walzen sorgen dafür, dass das Warmband hart und spröde wird. Als Verpackungswerkstoff ist es so noch nicht einsetzbar. Darum muss es erhitzt oder in der Fachsprache „geglüht“ werden. thyssenkrupp Rasselstein setzt dafür zwei Verfahren ein: das Haubenglühen und das Durchlaufglühen.
Beim Haubenglühen wird das aufgewickelte Band nach dem Kaltwalzen übereinanderliegend bei 600 bis 700 Grad unter einer Haube geglüht. Beim Durchlaufglühen wird das Material in senkrechten Schlaufen durch den Glühofen gezogen und dabei einer Temperatur von 670 bis 750 Grad ausgesetzt. Während der Prozess beim Haubenglühen mehrere Stunden dauert, liegt die Verweilzeit beim Durchlaufglühen bei unter zwei Minuten.
Die Anforderungen an das fertige Weißblech entscheiden, welches der beiden Verfahren angewendet wird.
Durch das Veredeln entsteht Weißblech
Kann das Material jetzt so bleiben? „Nein, da das Material noch zu starken Knicken und einem ungleichmäßigen Umformverhalten neigen würde, muss es in jedem Fall nachgewalzt werden“, erklärt Dr. Peter Kirchesch. Je nach Anwendungszweck kann das Weißblech in einem zweiten Schritt auch erneut einer Dickenreduktion um bis zu 43 Prozent unterzogen werden, fügt er hinzu.
Im letzten Verarbeitungsschritt wird aus dem Feinstblech im Veredlungsprozess das Weißblech – durchs Verzinnen oder Verchromen wird das Material zu dem, wie wir es kennen.
Apropos Weißblech – seinen Namen hat das Material von der weiß glänzenden Farbe, in der es schimmert. Aber egal, ob Zinn- oder Chromauflage: Der Veredelungsprozess stellt sicher, dass das Weißblech und damit Verpackungen wie Lebensmitteldosen, Kronenkorken, Verschlüsse oder Aerosoldosen optimal vor Korrosion geschützt werden.
Das Weißblech ist fertig
Nun wird das veredelte Weißblech wieder zu Coils aufgewickelt oder in Tafeln geschnitten. Danach wird es verpackt und an seinen Bestimmungsort – thyssenkrupp Rasselstein beliefert Kunden auf der ganzen Welt – verschickt.
„Und nun können daraus bei unseren Kunden viele Weißblechprodukte hergestellt werden “, sagt Dr. Peter Kirchesch abschließend. Er hat uns den Produktionsprozess im Video ganz genau erklärt. Dort seht ihr, wie groß die Anlagen sind, mit denen Weißblech in Andernach produziert wird.